機械技術2024年10月号
創成研削による内歯車加工の最新技術
遊星歯車機構は小型で高能率かつ高負荷容量なため、自動車の変速機やロポットの関節部に多く用いられている。 減速機を構成するリングギヤのわずかな幾何学的なひずみは、減速機構において加振力となり、騒音や振動の要因となる。 歯車精度に起因する騒音や振動は、従来の内燃機関用トランスミッションに比べ、少ない歯車の数で構成される電気自動車用 トランスミッションにおいて、より認知されやすくなる。このような背景から、リングギヤの品質に対する要求は厳しくなっており、 内歯車の高精度仕上げ加工のニーズがさらに高まっている(図1)。熱処理後のリングギヤの仕上げ工法として、 従来より歯溝を1溝ずつ加工する成形研削やホーニング、ハードスカイビングがあるが、加工能率、加工精度の課題があり量産現場へ の適用は依然として限られている。そこで当社は、世界初の量産向け内歯車創成研削盤「Z120A」(図2)を2009年に開発した。
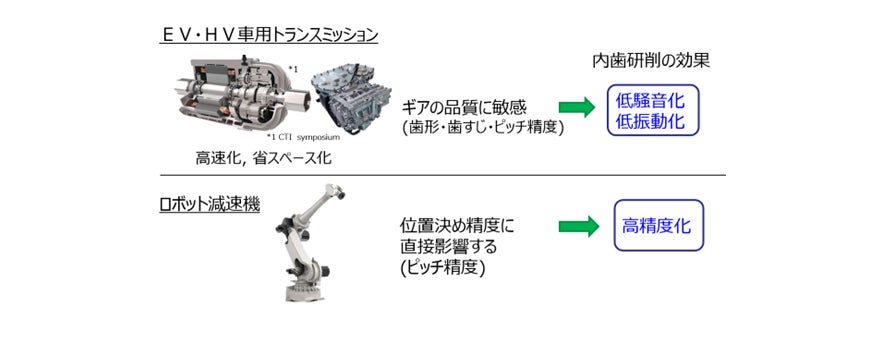
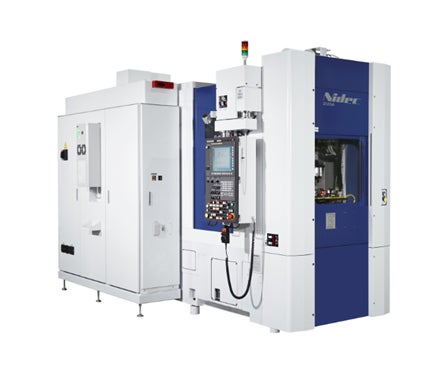
内歯車の創成研削
内歯車の創成研削は、量産に求められる歯車精度と生産性を両立する仕上げ加工法である。この高い生産性は、 高速高精度主軸と軸交差角に合わせた独自のといし設計により実現している。市場投入以降、この工法は実生産に用いられ、 効果が評価されてきた。本稿では、内歯車研削の高能率化やといし寿命延長への取組みと、今後のさらなる高精度化に向けた面粗さ向上に対する当社の取組みを紹介する。
Z120Aによる創成研削加工は、図3に示すように、樽形といしと被研削歯車(ワーク)がかみ合い、創成運動を行うことで歯面を仕上げる。 研削性(切れ味)や研削比(耐摩耗性)を上げるには、研削速度を上げる必要があり、といし軸とワーク軸は高速回転させ、同期制御を行う。 また、といし軸とワーク軸の軸交差角を大きくすることで、研削点でのすべり速度が大きくなる。研削性の向上により、歯形や歯すじ形状の修正だけでなく、 ピッチ精度を含めたすべての歯車精度を向上することが可能となり、工具寿命を延長することができる。
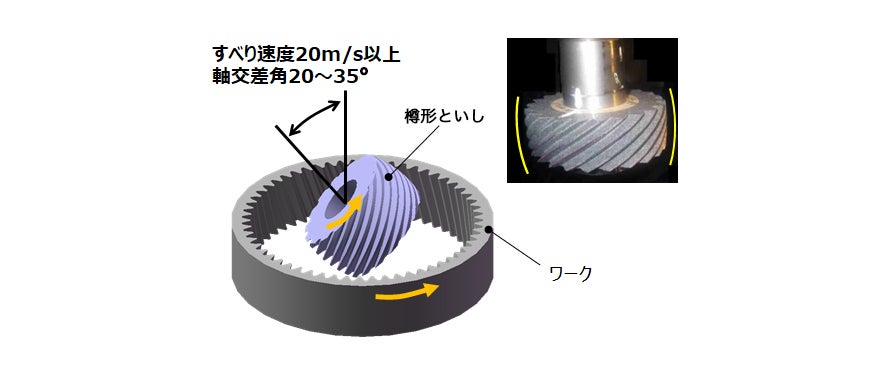
内歯車研削の高能率化、工具の長寿命化の取組み
外歯車の加工では、ワークに対して大きな工具(といし)が使用できるため、工具シフトを行い、工具が摩耗した際に接触ポイントをずらして工具寿命を延ばすことが可能である。 一方、内歯リングギヤの加工では、「干渉による制約を受けワーク内径より大きい工具を使用できない」、「工具シフトができないことから、 工具寿命を延ばすためには工具の耐摩耗性向上が必須」といった条件がある。そのため当社の内歯車創成加工では、従来、耐摩耗性の高いcBNといしを主に採用してきた(図4)。 近年、ワークサイズの大径化や薄肉化により、研削仕上げの除去量が増加している傾向がある。それに伴い、より高能率、高負荷条件での加工ニーズが増加している。cBNといしは、 一般といしに対して研削抵抗が高い。特にドレス直後の研削抵抗が高いためドレス直後は加工能率を下げての加工(スロー研削)が必要となる特性がある。 高負荷条件では研削抵抗が高くなり、と粒脱落によるといし摩耗により、本来のcBNといしの耐摩耗性が発揮できなくなる。一方、切れ味の良い一般といしでは、 といし仕様のチューニングにより高負荷条件でcBNよりもといし寿命が長くできるものも開発されてきた。
ここでは、従来の2倍の研削条件(図5)でcBNといしと一般といしで連続加工を行った事例を示す。cBNといしに対して、一般といしの方が歯形形状の変化が少なくといし摩耗が少ない (といし寿命が長い)結果となった(図6)。一般といしで連続加工した歯車チャートを示す(図7)。ドレス後1個目からドレス後140個目まで、歯形と歯すじの形状はほとんど変化は 見られず良好な結果が得られた。以上のことから、一般といしにおいても従来の2倍の高能率加工が可能となり、サイクルタイムの低減とワーク1個当たりの工具費低減が可能となった。
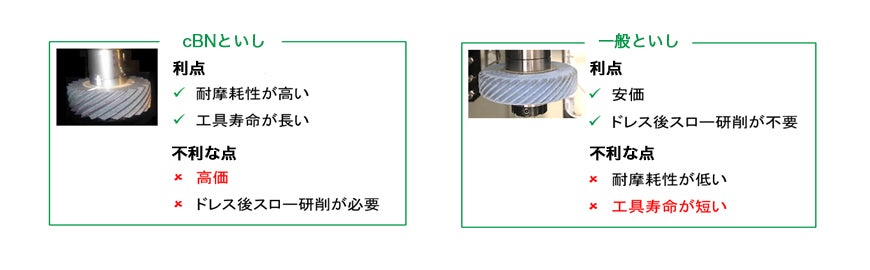
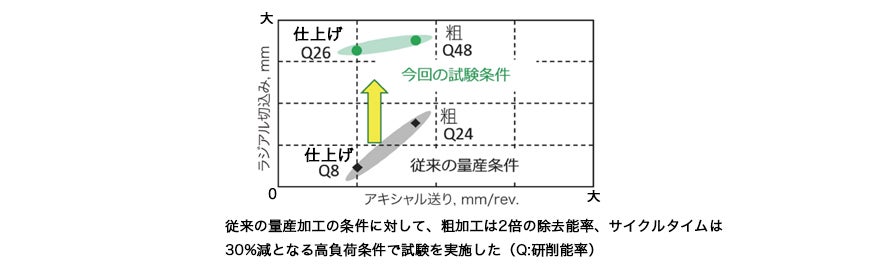

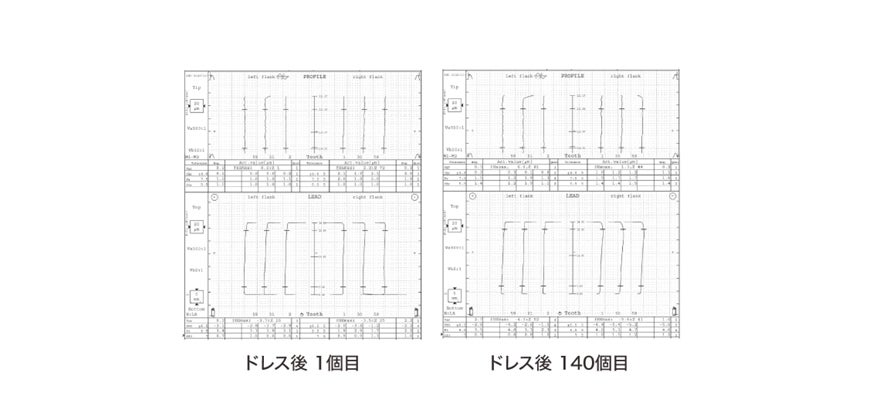
内歯車の弾性といしによるポリッシュ研削
ギヤの滑らかな表面性状は、騒音や振動、効率の改善とともに、歯車の耐久性を向上することが期待される。外歯車の仕上げ加工には、高生産性と高品質を兼ね備えた創成方式の 研削とポリッシュ(研磨)加工がすでに量産において実用化されている。研削加工は要求される幾何形状を得るために、ポリッシュ加工はRa0.1μm、Rz1.0μm以下の表面粗さを 得るために用いられている。内歯車についても、表面性状の改善により、外歯車と同様の効果を得られることが期待されるため、といしでは創成方式の研削とポリッシュ加工の 開発に取り組んでいる。面粗さの目標は外歯車と同様のRa0.1μm、Rz1.0μm以下としている。
ポリッシュ研削には、弾性率の低いといしを使用した。一般といしでの加工試験と同じ諸元のリングギヤで実加工を行った。結果、通常の歯車研削加工では、 加工歯面の表面粗さはRa0.3μm程度であるが、ポリッシュ研削を行うことで表面粗さ0.1μmを実現できることが確認できた(図8)。また、 ポリッシュ研削を実施してもポリッシュ研削前後で歯車の歯形・歯すじ精度への影響変化はほとんど見られなかった(図9)。適切な弾性率の弾性といしを用いることで、 歯面の面粗さは向上させるが、歯面形状は変化させることなく研削することができる。
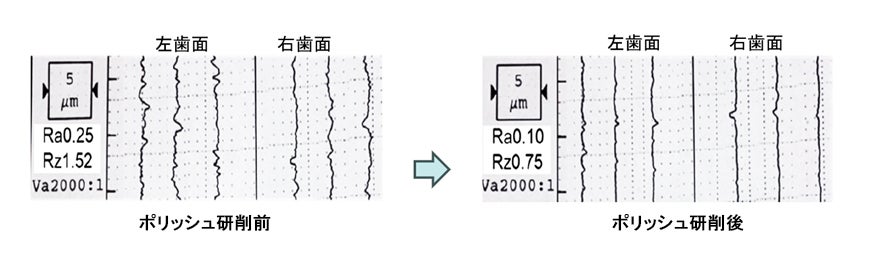
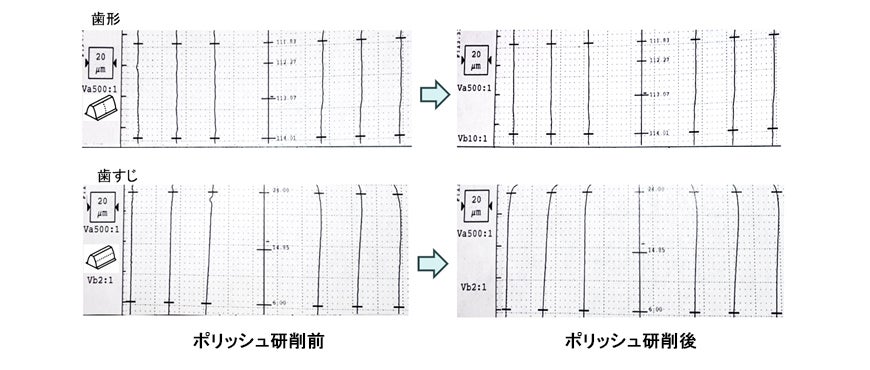
今後の取組み
内歯車をより高精度・高能率に仕上げる加工技術に対する取組みは継続して行っていく。特に内歯車のポリッシュ研削については、新たな加工法であり、 量産への対応に向けて、ロバスト性の評価を実施する。今後も新たな工法を提案し、歯車加工現場のニーズに応えられる製品、加工技術の開発を進めていく。