機械技術2024年3月号
EV化に適応した最新の歯車加工技術の取組み
近年CO 2 排出量が年々拡大してきており、より一層、地球温暖化が進みつつある。海水の温度は上昇し、海水面水位の上昇など、地球がめまぐるしい変化を遂げている。地球の温暖化に対して改善の手段としてCO 2 削減を進めようとしている。自動車業界では内燃機関からCO 2 削減が期待されるハイブリット車(HV)が普及し、さらに電気自動車(EV)化が進みつつある。日本ではEV化は緩やかであるが、世界では産業革新を狙って新規参集するメーカも増えている。EV化が進むにつれて、従来のような多段のトランスミッションではなく、2段程度の減速機構をもつシンプルな構造のEV用トランスミッションの普及も進みつつある
このトランスミッションに使用されるギヤは少なくなったものの、EV化により内燃機関がエンジンからモータにとって代わることで音のする装置がなくなり、車内の静音化がよりシビアに求められるようになった。EV用トランスミッションの静音化に対応するため歯車の高精度化がより一層進んできている。本稿では、EV化に適応した当社の最新歯車加工技術の取り組みについて歯車の加工事例を挙げて紹介する。
EV化による面取り加工の高品質化
歯車における面取り加工は、従来の自動車用トランスミッションギヤでは組立時に面取りができていればよいレベルであった。EV化に伴い歯車の高精度化が進み、図1に示すように熱処理後に歯車研削・ホーニング工程が増加すると、フレージング工法による面取りでは歯面側に膨らんだバリによってといしに局部的な摩耗が発生するため、仕上げ工程での加工精度に問題が生じる要因となっていた。これを改善するために、塑性変形で面取り角部に膨らみが残るフレージング工法より、膨らみが生じない切削による面取り工法のニーズが高まってきた。
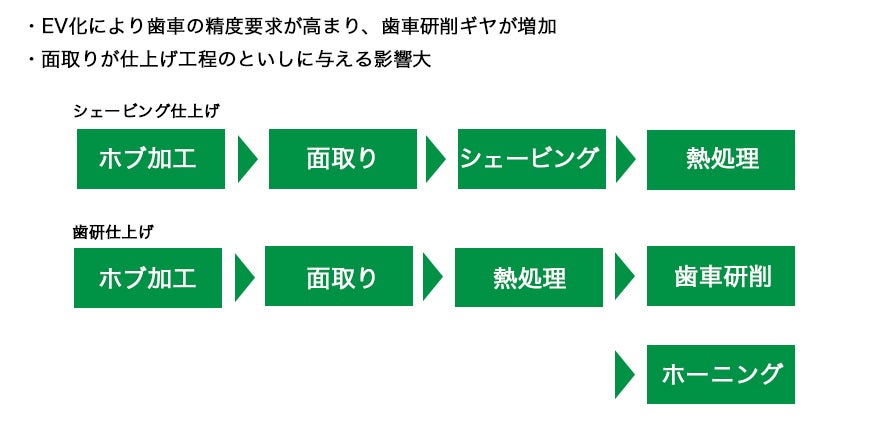
このニーズに対応するため、当社ではホブカッタのような回転工具による切削面取り加工ができる切削面取り盤「CF26A」を開発した。CF26Aによる切削面取り加工事例についてフレージング工法と比較しながら紹介する。フレージング工法と切削面取り工法の面取り形状図を示す(図2)。
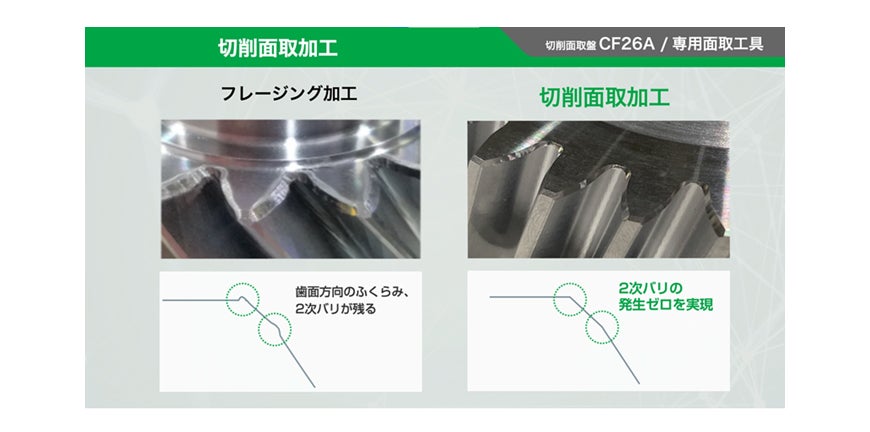
フレージング工法とは、フレージングカッタをギヤ歯面に押し付けて塑性変形させることで面取り形状を形づくる工法で、塑性変形する際にギヤの端面側と歯面側に膨らみが生じる。この工法のメリットは、一定レベルの面取り形状をつけることができ、かつフレージングカッタの寿命が長く工具費を抑えられる点である。デメリットは、ギヤ端面側に膨らんだバリはバイトカッタで除去できるが、歯面側に膨らんだバリは除去できないため、そのままとするか、ホブ加工でもう1度さらえ加工して除去しなければならない点である。また、バイトカッタによるバリ除去工程では、バイトカッタが摩耗してくると2次バリが発生するためバイトカッタの摩耗管理が必要となる。
これに対して、切削による面取り工法では、ホブカッタのような回転工具を使い面取り部を創成加工で除去するため、面取りの両角部に膨らみはなくバリの発生もない。また、バイトカッタも使用しないため、ギヤ端面の形状もきれいな状態を保つことができる。さらにフレージング工法では加工が難しい歯底面取りができるメリットや、1mm以上の面取り幅を安定して加工できるメリットがある(図3)。このため、EVギヤのような高精度仕上げ加工を要する歯車には有効な工法と言える。
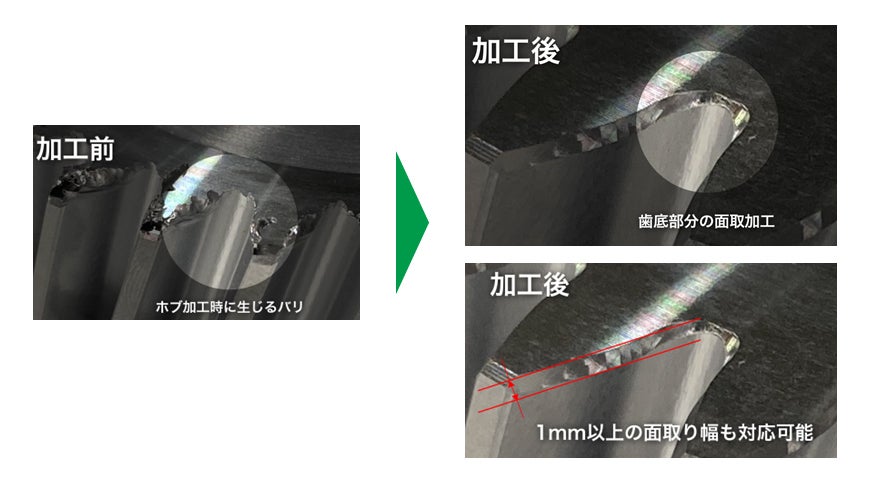
歯車研削加工の高精度化と最適化
1.ポリッシュ研削
EVギヤでは従来のギヤよりも高い静粛性を求められることから、かみ合い時の振動を低減するため歯面の面粗さ向上や、かみ合い時に振動の原因となる周期的な歯面の形状誤差の低減が求められている。歯面の面粗さを向上させる方法として、歯車研削加工後にポリッシュ用といしを用いた表面仕上げ加工(ポリッシュ研削)が注目されている。
通常の歯車研削加工では、高能率で加工できるねじ状といしを用いた創成歯車研削が一般的には採用されている。ポリッシュ研削は、通常の歯車研削用といしと弾性率の低いポリッシュ用といしを結合させたといし(図4)を使用する加工方法で、通常の歯車研削後ワークを脱着することなくポリッシュ用といしで仕上げることができるため、高精度な仕上げ加工が可能である。
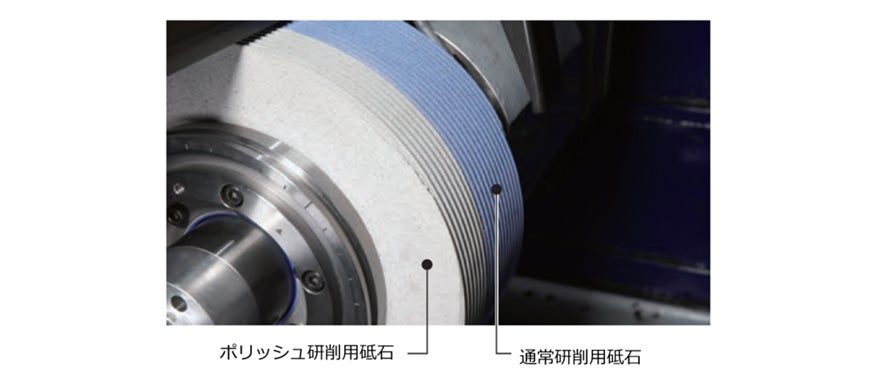
当社の加工事例によると、通常の歯車研削加工では、加工歯面の表面粗さはRa0.3~0.4μm程度であるが、ポリッシュ研削を行うことで表面粗さRa0.06μm以下を実現し(図5)、圧縮残留応力は通常研削の約1.7倍となった。また、ポリッシュ研削を実施してもポリッシュ研削の前後で歯形・歯すじ精度への影響はほとんど見られなかった(図6)。適切な弾性率の弾性といしを用いることで歯面の面粗さは向上させるが、歯面形状は変化させることなく研削できる。
ポリッシュ研削を行うことで歯車表面の面粗さを向上させ、ギヤのかみ合い時の静粛性の向上が図れる。また、圧縮残留応力が付与されることで歯車の歯面強度向上を図ることも期待できる。
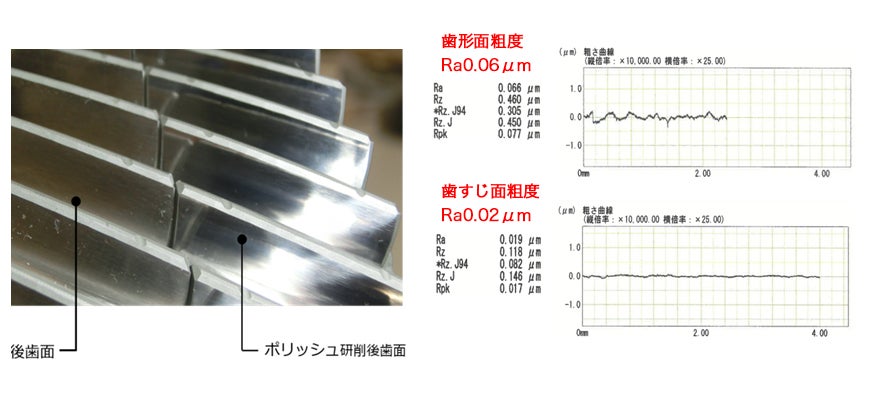
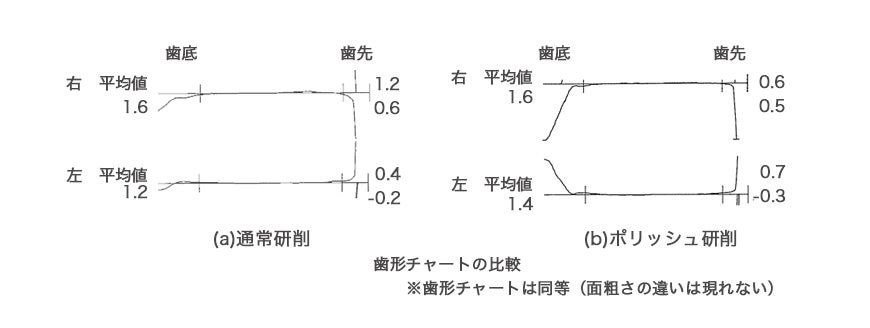
2.バイアス修整機能
自動車のトランスミッションなどの歯車では、小型化や静粛性の向上を目的として最適な歯車のかみ合い状態を実現できる複雑な歯面形状が要求される。歯車研削の工程で、はすば歯車の歯すじ方向にクラウニングを付与した際に、歯幅方向で歯形の圧力角が変化して歯面にねじれ(バイアス歯面と呼ばれる)が発生する。このバイアス歯面を修整することでかみ合い時の振動を低減できることが知られており、近年の自動車の電動化の中でバイアスを修整する技術は不可欠となってきている(図7)。
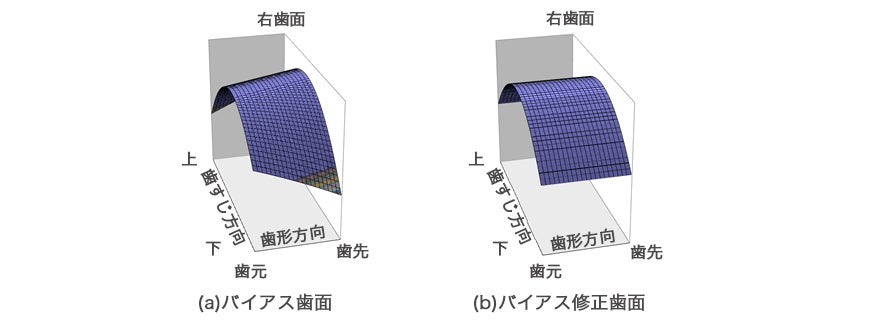
バイアス歯面を修整するには、通常のドレス動作とは異なる動作でといしを成形する。ドレス動作において、といしの幅方向に異なる歯形形状をつくり込み、要求に合った歯形のといしを加工時に使用することによって任意の歯形形状を得ることができる(図8)
。
当社の歯車研削盤ZE16C/26Cではロータリドレッサの旋回機構を新たに開発することで、これを実現した。
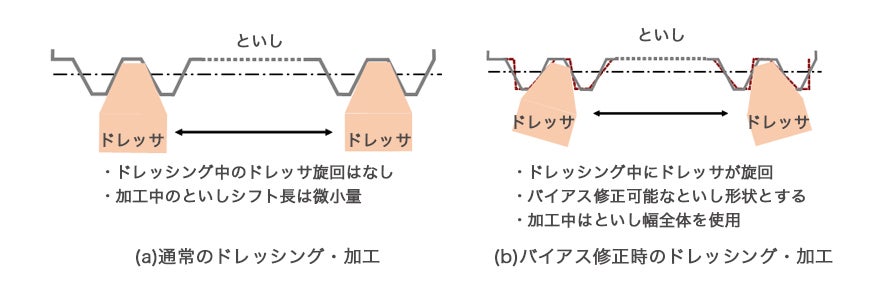
歯車研削盤ZE26Cによるバイアス修整の加工事例を紹介する。歯すじにクラウニングを付与すると、バイアス修整前は歯車の上部、中央、下部の歯形はそれぞれ異なる歯形となる。これにバイアス修整機能を用いて歯車研削すると歯車の上部、中央、下部の歯形をすべて同じ歯形にすることができる(図9)。
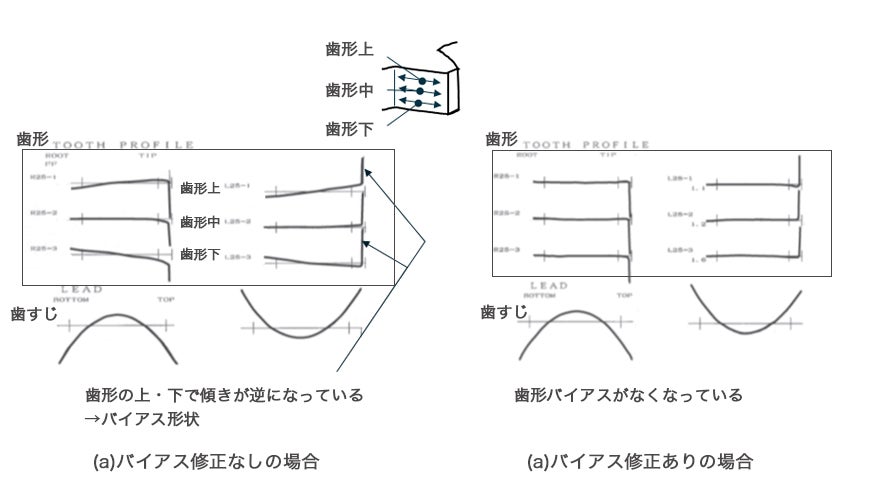
この機能を活用することで、歯車の歯幅の全領域で狙った歯形に制御できる。これによりかみ合わせの歯当たりを均一化でき、かみ合い時に発生する振動を軽減することでトランスミッションの振動を低減し静粛性を向上させる。このような歯車がEVの歯車には適用されている。当社では、といしの幅方向の歯形形状を荒加工で使用する領域と仕上げ加工で使用する領域で異なる形状にすることで、といし寿命を延ばす取組みを行っており、バイアス修整時の工具費削減にも貢献できる。
3.ポリッシュ研削とバイアス研削の組合せによる影響
EV化に必要不可欠な高精度な歯車をつくるための仕上げ加工技術として、歯車研削のポリッシュ研削とバイアス修整機能について説明した。この機能を併用するには、通常といしとポリッシュ用といしを結合した2連といしを使用してバイアス修整を行う必要がある。ポリッシュ用といしでバイアス修整ができるほどの修整力を持たせることができないため、両方の機能を実施するにはといし幅の制限が大きく、といし寿命に影響する。この問題は今後の課題として検討を進めていく。
現時点では両方の機能を要求されることは多くはないが、今後はこのニーズが増えてくると予測されるため、要求される加工技術に対して、実現できる工具と機械の開発を進めていきたい。
自動車のEV化や低燃費・低騒音への要求は今後ますます高まり、歯車加工における高精度化・高能率化の傾向はさらに続くと考えられる。高精度化・高能率化への取組みとしては、現時点で対応できる機能をすべて網羅できる製品開発を継続していく。一方でEV化に伴いトランスミッションの方式が変化すると考えられる。当社では時代の要請に応じて歯車の加工技術をより一層磨き、また、どのようなトレンドにも柔軟に対応できるよう、加工を支援するアプリケーションの充実や顧客ニーズに応える製品開発を今後も進めてゆく。