Implemented Solutions
Automated Transportation Robot Drive Module
- NEEDS
- Save labor of warehouse transportation, and improve its efficiency.

- SOLUTION
- Develop a high-precision, high-efficiency, and low-cost automated transportation robot module.
Generate synergies within the Nidec Group to develop a high-efficiency drive module.
Products to support the constantly expanding e-commerce market
Here’s a scene at a major online shipping company’s distribution center: More than 100 automated transportation robots crisscrossing a huge warehouse entirely lined with merchandise-stored shelves, picking up and deliver one of them to distribution personnel, or pickers, who pick up merchandise from the shelf, as the robots return to their original locations, and put down the shelves, to quickly follow a new order and move to the next shelf.
A survey conducted by Japan’s Ministry of Economy, Trade and Industry shows that the scale of the Japanese domestic B-to-C-EC (consumer-oriented electronic commerce) market is expanding year after year, and reached 19.4 trillion yen in 2019. The rate of the market’s growth is increasing annually as well, with no sign of peaking out. Major online shipping companies are urgently expanding and streamlining their equipment, while being focused on automating their transportation systems to solve chronic labor shortage.
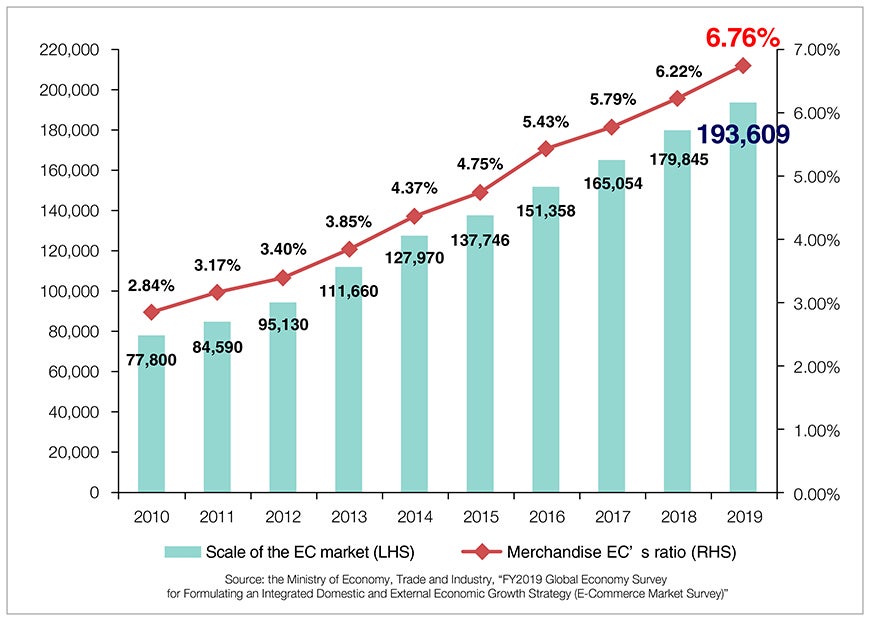
(Source: the Ministry of Economy, Trade and Industry, “FY2019 Global Economy Survey for Formulating an Integrated Domestic and External Economic Growth Strategy (E-Commerce Market Survey)”)
A reducer developer and manufacturer, NIDEC DRIVE TECHNOLOGY works with the Nidec Group’s motor-making companies to supply drive modules for those automated transportation robots that support this online shipping market.
Utilize high-precision gear-machining technologies to develop low-backlash planetary gears
NIDEC DRIVE TECHNOLOGY has long been manufacturing planetary gears for servo motors used for various industries. For applications that require extremely accurate positioning, reducers’ backlash must, of course, be small. It is to meet this request that the company has been focused on the high-precision machining of its gears. When it received an inquiry from a robot manufacturer on a drive module for automated transportation robots to operate in an online shipping business’s warehouse, NIDEC DRIVE TECHNOLOGY fully demonstrated its technological capability to successfully develop a low-backlash planetary gear. By collaborating with Nidec Motor (US), a Nidec Group company, NIDEC DRIVE TECHNOLOGY provided a motor-reducer-integrated low-backlash, high-efficiency drive module, which contributed greatly to high-precision positioning and long-hour battery use. From 2015 to December of 2020, the company shipped a total of approximately 1.05 million units of this drive module, which are used at distribution centers all over the world.
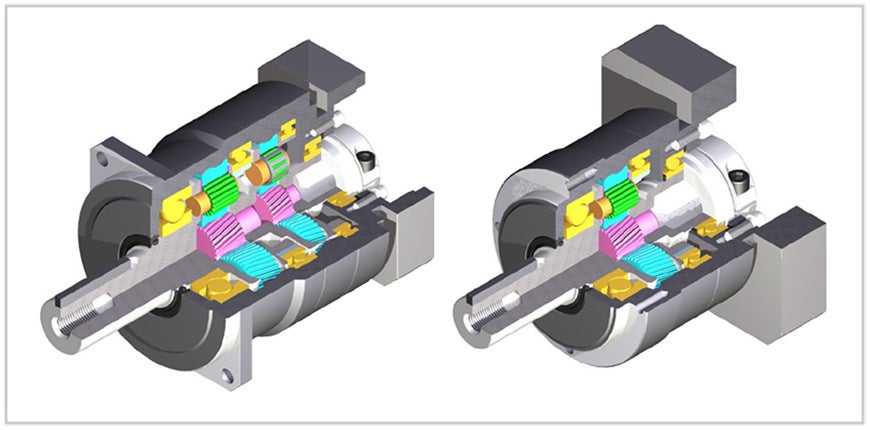
Collaborating with the Nidec Group’s motor manufacturers to meet miniaturization and cost reduction requests
Sparked by the high reputation it received from the business for an online shipping company’s warehouses, NIDEC DRIVE TECHNOLOGY now works with various motor manufacturers of the Nidec Group, supplying reducer-motor-integrated drive modules globally.
The two most common requests that NIDEC DRIVE TECHNOLOGY receives on its drive modules are to make them light, thin, short, and compact, and to reduce their cost. To meet these requests, the company provides solutions based on synergies in the Nidec Group.
One of the solutions is to integrate a reducer with a motor.
Normally, to transmit power from a motor to a reducer, the shaft of the motor is connected to its reducer with a connecting shaft. A connecting shaft can combine a reducer with a motor even if they are developed completely separately; however, such combination increases the number of required components, and makes the finished product long. Thus, a process was adopted where NIDEC DRIVE TECHNOLOGY would produce the shaft itself, a motor’s central component, gear-cut it, and deliver it to the Nidec Group’s motor-manufacturing companies, which would use the shaft to produce motors. With this method, NIDEC DRIVE TECHNOLOGY would send the motor-manufacturing companies reducers just about when motors were made, and those sun-gear-equipped motors were combined with the reducers to become drive modules. This production process enabled modules to be compact, and require fewer components to reduce cost.
In addition, in a joint project with Leroy-Somer Motors & Drives CTD (UK), another Nidec Group company, a gear’s configuration was revised and a motor’s output rotation was adjusted to optimize the product as a geared motor.
For reducers, which had normally been used for travelling axes, two gear trains were used to achieve a reduction ratio of 1/20, and they were connected to wheels with output axes. In its attempt to achieve further miniaturization and cost reduction, NIDEC DRIVE TECHNOLOGY achieved a reduction ratio of 1/9, using only one gear train, while adopting internal rotation specifications which enabled a reducer’s case to output rotation, to successfully develop a reducer that fits inside a wheel (See the chart on the next page). In the development of this reducer, NIDEC DRIVE TECHNOLOGY collaborated with Leroy-Somer Motors & Drives CTD, a motor manufacturer, and suggested a specification change. After adjusting the output, the two companies developed a combination which keeps the speed reasonable while securing a sufficient amount of torque, succeeding in reducing their geared motor’s size significantly, and slashing cost.
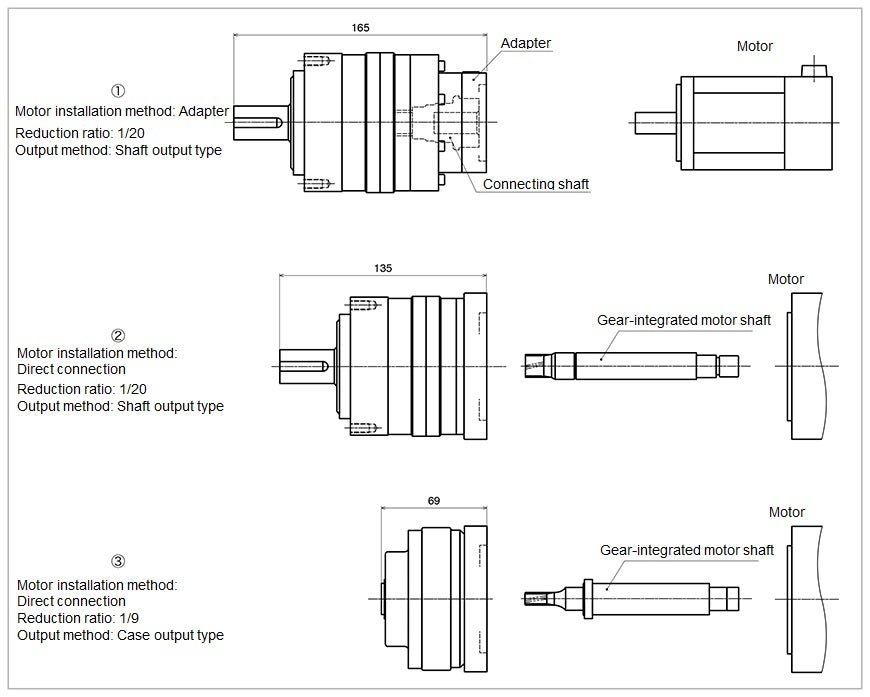
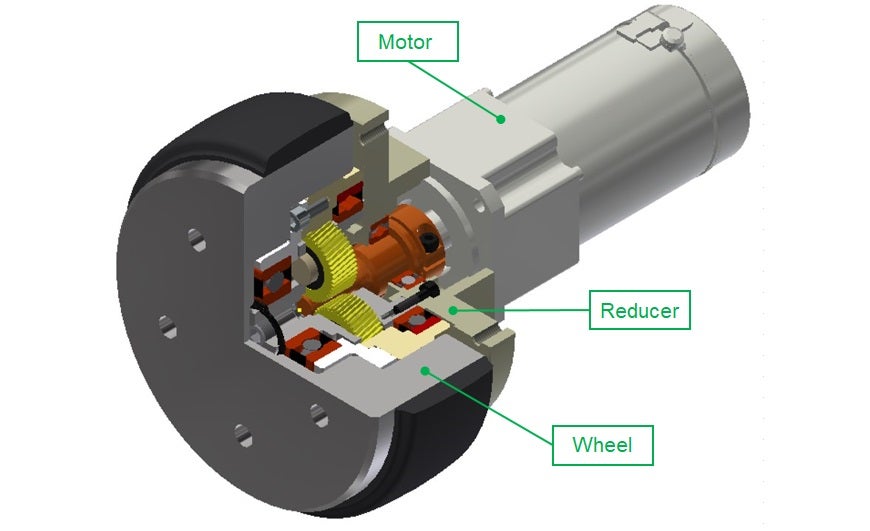
As the online shipping market continues to expand, to further improve logistics efficiency, NIDEC DRIVE TECHNOLOGY will further forge its ties with motor-making Nidec Group companies to develop higher-efficiency geared motors, while contributing to the creation of cutting-edge logistics warehouses.