Nidec's Technical Capabilities
Using molding technology to make automotive camera lenses plastic of glass-level quality
Nidec has been producing brushless DC motor-based fan motors – products that generate wind, transfer heat, and generate pressure – at full scale since 1982. With a wide range of product lineup, and thanks to the product-developing technology supported by supercomputer-based fluid analysis and other elements, and the long-accumulated knowhow of cost-reducing production technology cost, Nidec’s fan motors are used in a variety of businesses.
This section features fan motors’ roles, major applications, and types.
- NEEDS
- Take advantage of plastic’s merits for the growing automotive camera market

- SOLUTION
- Using plastic to realize glass-level performance
Creating heat- and scratch-resistant plastic lenses
As advanced safety technology becomes popular and autonomous driving technology evolves, many newly launched vehicles are installed with cameras. With automotive cameras’ lenses generally made of several lenses, plastic, aspherical lenses are used widely for cost-saving purposes. However, in almost all cases, the outermost lens has had to be made of glass, as its surface is required to be strong. Thus, Nidec Instruments utilized its plastic lens technology to successfully develop a fish-eye lens unit for automotive cameras, with the use of a super-hard outermost lens (L1).
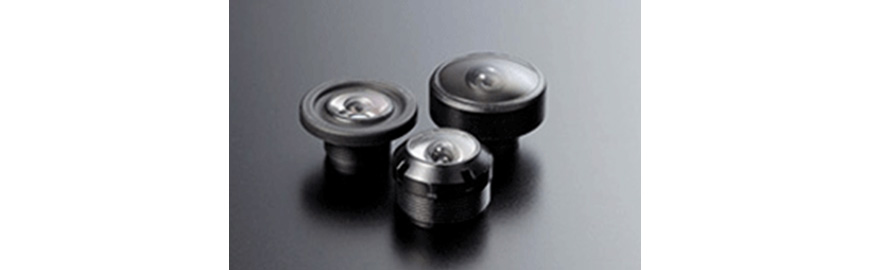
Fish-eye lenses, which capture an image with an ultra-wide angle, are used in, among others, surround view monitors that show the environment around the vehicle. The lenses, installed on the vehicle’s surface and exposed to the outer air and heat, are required to be heat-resistant. Further, the L1 lens must be reliable – tremendously more so than smartphone and other cameras – to stay unscathed even after being exposed to dust, hit by a car washer’s brush, etc. This is why scratch- and heat-resistant, and highly reliable glass lenses have been used for the automotive camera’s L1 lens so far.
Taking advantage of the plastic lens in a joint research with Nidec Keihanna Technology Center (NKTC)
To secure the surface strength of glass, we newly adopted as base material heat-resistant acrylic resin that is both super-hard and heat-stable. Though plastic, the lens is super-hard and significantly more heat-resistant than its predecessors. Additionally, with its surface hard-coated (HC) and covered with an antireflective (AR) film, the lens boasts a glass-equivalent reflectance of 1% or less while maintaining its strength.
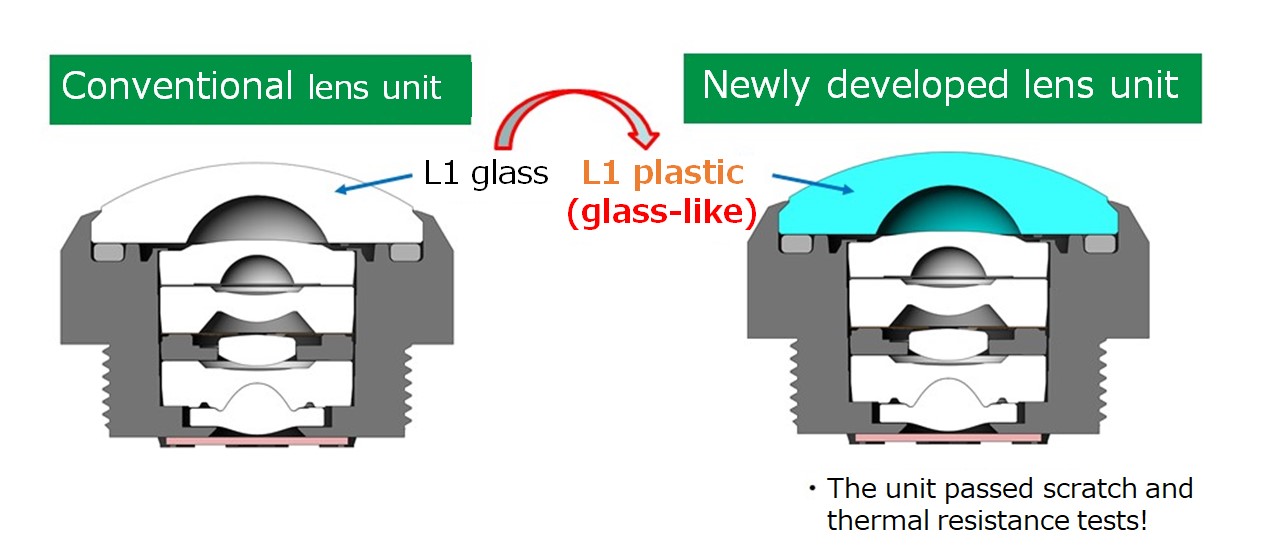
As its name suggests, the hard coat (HC) is to improve a substance’s hardness. Placed between the base material (organic) and the AR film (inorganic), the HC serves as a shock-absorbing material of the two. While the base material is thermally elastic, the AR isn’t. This is why it is necessary for the HC to maintain its hardness while keeping its shock-absorbing function as well. To secure these roles of the HC’s, we underwent a process of trial and error to search for an optimum configuration of inorganic materials, thickness of the HC, and number of layers for coating, before seeing the HC achieve the ideal super-hardness.
Not only does the AR film reduce reflectance, it helps the lens harder. However, merely improving its hardness and adding layers to it would only make the lens prone to cracks. This is why we conducted optical condition-based simulations and actual tests repeatedly, and created multiple layers of the AR film, to finalize its film-forming conditions. Then, combining it with the aforementioned HC, we successfully improved the pencil hardness to 6 – 7H.
The HC and the AR film with these high functionalities are the results of our joint research with NKTC. To identify the optimum solution out of tens of thousands of possible combinations of material compositions, film thicknesses, numbers of layers, and engineering methods among others, we needed the technological center’s in-depth knowledge on simulation and production technologies. Now, the lens, which was created based on the One Nidec policy that established the collaboration between Nidec Instruments, a molding technology expert, and NKTC, is bringing fresh air into the world of automotive cameras.