加工事例 - 精密加工機の加工事例 - 小型精密加工機μV1
サファイア、グラッシーカーボン、石英ガラスの加工
※本記事は、「機械技術2011年11月号」に掲載した論文です。
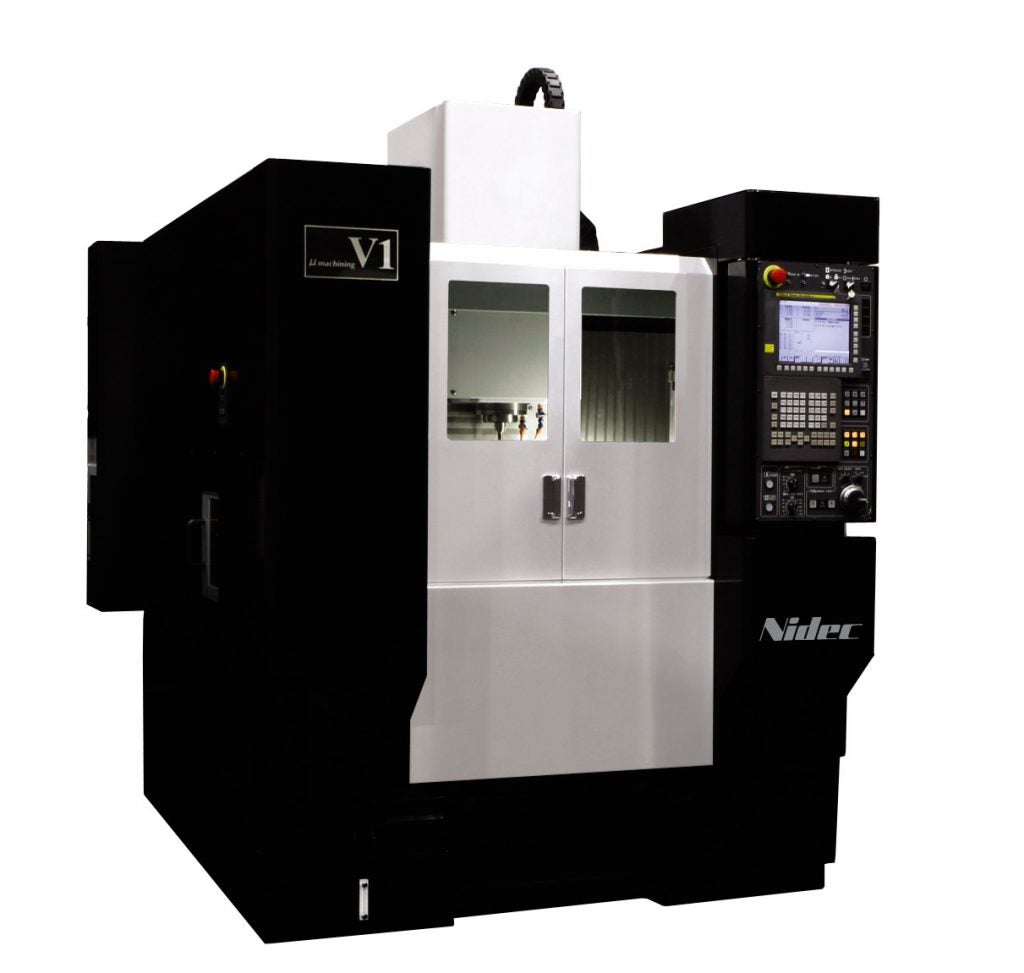
はじめに
IT、光学、医療機器、半導体デバイス等の機器の小型・軽量化や高機能化に伴い、これらを構成する部品の高精度化や微細・精密化の要求が益々高くなってきている。また耐熱、耐水・油、耐薬品性、耐食性などの目的から、使用する材質もセラミクスや石英ガラスといった硬度が高くて脆い、いわゆる難削材が増えてきている。
当社においても、それらの要求に応えるため小型精密加工機μV1を用いて、微細精密加工や難削材加工に取組んでいる。本稿では、これらの加工事例と加工機の特長について紹介する。
小型精密加工機μV1の特長
微細精密加工や難削材加工においては、微細な形状や材料表面の損傷を防ぐため、非常に小さな切込み、取り代にて加工することが多い。そのため加工機に対しては、主軸や送りの振動が無く正確に動作すること、加工中の熱変位が無く安定していることといった動的な運動精度の高さが求められる。
μV1においては、主軸の熱変位を抑えるため、主軸のケーシングである外側のジャケットを冷却するのみではなく、高速で回転する主軸の内部をも冷却し、また軸受を当社独自の方式で特殊潤滑することにより、発生した熱を強制的にすばやく除去している。主軸の各部の熱変位を抑えることにより、軸受の予圧変動を無くし、低速から最高回転速度40,000min-1までの全域において、振動を極限まで抑え込んでいる。
また送りについては、機構自体に振動の発生源が無く、かつ外部からの振動に対して高い減衰性を持つ滑り摺動面を採用し、振動を抑制している。
機械本体の熱変位に関しては、構造体の熱容量を大きく取り、更にコラム内に熱容量の高い媒体を封入させることで、環境温度のふらつき等の変化に対してロバスト性を高めている。
工具測定の高精度化
前述した通り、微細精密加工や難削材加工においては、非常に小さな切込み、取り代にて加工することが多いため、工具先端の正確な測定、位置把握も重要となる。
当社においては、機上工具測定の高精度化のため、高解像度CCDカメラを使用した「撮像式工具測定システム」を独自開発し、μV1に搭載している。撮像式工具測定システムは、従来の工具をセンサーに接触させて測定する「接触式」、レーザーを工具で遮光させることで測定する「レーザー式」のそれぞれが測定原理上持つ下記の誤差要因を解消することができる。
【接触式の誤差要因】
- 接触の衝撃による工具先端やセンサーの測定面の損傷、損耗による誤差
- 主軸停止→回転による熱変位等による誤差
レーザー式の誤差要因 - レーザーを当てるポイントと真の工具先端とのずれによる誤差
- 工具先端の形状の違いで発生するレーザーの遮光率の差による誤差
更にカメラで連続的にデーターを収集するため、機械や工具の熱変位の時間的な挙動を測定することができる。このことにより、機械や工具の熱変位がサチュレートして安定したことを把握することができ、その後の安定した領域で誤差なく加工することが可能となる。
微細精密加工事例
サファイアへの微細溝加工
サファイアは新モース硬度で12の硬さを持ち、広い透過範囲や高い熱伝導率などから過酷な環境で使われる機械部品や光学部品として使用されている。
サファイアより硬度の高いダイヤモンドの工具を用い、ウェーハ形状のサファイア素材の上面に回路を模した溝形状を加工した。使用したダイヤモンド工具を図1に、加工後のワーク写真を図2に示す。
一回の切込みが0.001mmと非常に小さく、刃先の位置精度、振動、繰返しの再現性等が高度に求められるが、形状や表面の損傷も無く加工することができた。
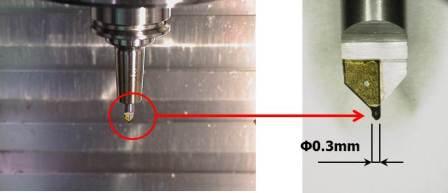
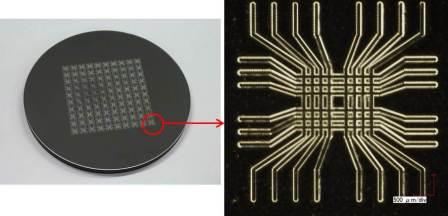
グラッシーカーボンへの穴加工
新モース硬度で10の硬さを持ち、優れた耐熱性、耐薬品性を持つグラッシーカーボンは、電気伝導性にも優れ、カーボン粉が出にくいことから、各種計測機器や半導体関連にも用いられている。
サファイヤと同様、ダイヤモンド工具を用いて貫通穴および形状加工を実施した。加工後のワーク写真を図3に示すが、これも形状等の損傷なく加工することができた。
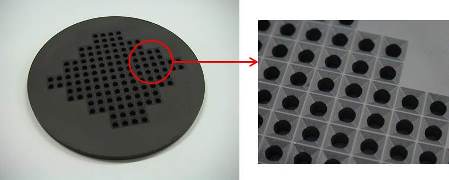
石英ガラスへの微細溝加工
優れた耐食性、耐熱性を持ち、非常に透明度の高い石英ガラスは、光学、化学、医療など様々な分野で用いられている。
サファイアと同様、回路を模した溝を損傷することなく加工した。ワーク写真を図4に示す。
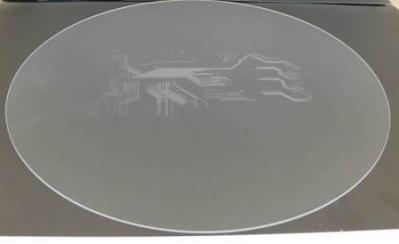
まとめ
小型精密加工機μV1および撮像式工具測定システムの特長とこれらを用いた微細精密加工の事例を紹介した。難削材への微細精密加工は、高価な工具が必要であるなど様々な問題もあるが、切削加工であるが故のメリットも多数あると考えている。今後も様々な要求に対応し、微細精密加工に取組んでいく所存である。
※「機械技術2011年11月号」掲載論文