加工事例 - 精密加工機の加工事例 - 小型精密加工機μV1
高精度金型加工の提案(1) 加工面段差の検証
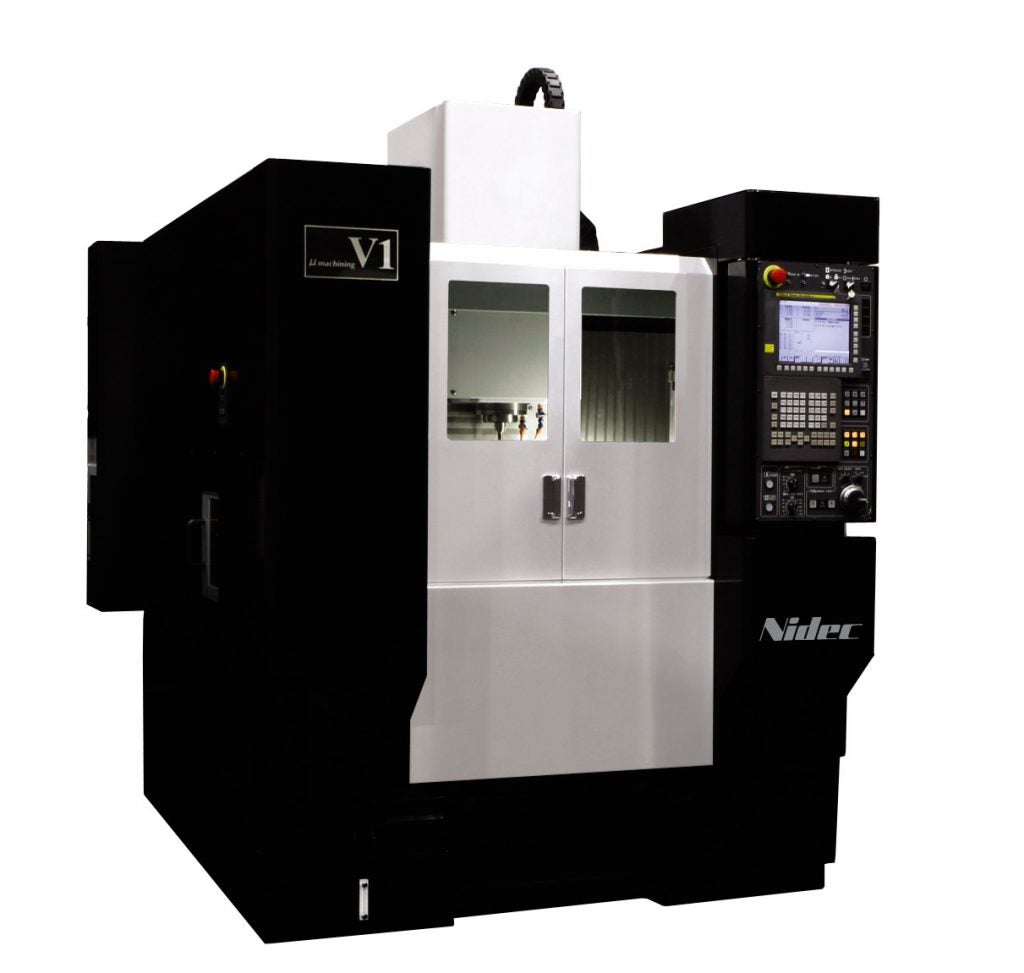
※本記事は、「型技術2011年2月号」に掲載した論文です。
はじめに
IT、光学、医療機器、半導体デバイス等の部品の複雑化、高性能化に伴い、これらの部品や金型を加工する工作機械の高精度化の要求が益々高くなっている。工作機械の位置決め精度に関しては、送り機構の機械要素技術、制御技術等の発展により、サブミクロンから数十nmのレベルの物も市場に出るようになってきた。
しかしながら、実際の加工点は工具とワークであり、この工具先端位置およびワーク位置の把握、制御ができなければ、高精度加工は不可能である。工具とワークはユーザーにて準備、運用することから、従来これらの測定に関しては、精度は測定器メーカーの所掌、測定の運用はユーザーの所掌として、工作機械メーカーとして深く取組んでこなかった。
当社は、これら工具およびワークの測定を含めたトータルの加工精度の向上を目的とした機上測定システムである「撮像式工具測定システム」を独自開発し、先般開催された第25回日本国際工作機械見本市(JIMTOF2010)にて小型精密加工機μV1へ搭載し出展した。本稿ではこの撮像式工具測定システムの特長とこれを用いた加工事例について紹介する。
撮像式工具測定システムの特長
一般的に工具長測定装置として使用されているものは、接触式とレーザー式が知られている。
接触式の場合、工具(主軸)を回転させながら測定できないため、測定後、加工のために工具を回転させた際の主軸や工具の熱変位が加工誤差として現れてしまう。
レーザー式は、工具を回転させながら測定が可能であるため、上記の誤差を抑えることができるように思われるが、熱変位には時間的な変化があり、変位が落ち着いて安定する前に測定をしてしまうと、その後の変位がやはり誤差となってしまう。
この問題を解決するため、当社では「撮像式」という新たな方式を採用した。測定原理は、図1に示すようにLED照明とCCDカメラの間に工具を入れ、工具を撮像し、取得した画像をデジタル処理して工具先端の位置情報を取得する。非接触であるため、工具を回転させながら測定することができるのは勿論のこと、従来技術の様な瞬間的な測定だけではなく、CCDカメラを用いることによって、連続的な測定を行うことができる。この連続的な測定により、主軸や工具の熱変位、機械の姿勢変形なども含めた工具先端の挙動を把握することができ、自動で変位が安定したことを判定して測定を終了させ、加工を開始する“システム”を構築した。
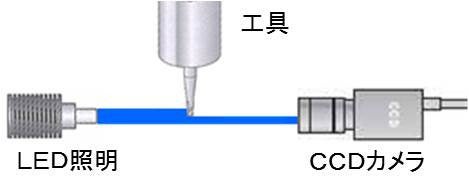
加工事例
金型加工、特に直彫り加工においては、一つの金型を加工するのに径や形状の異なる複数の工具を用いる場合も多く、また高硬度材を加工するために工具の摩耗も起こりやすく、更に加工が長時間に及ぶ場合も多い。この場合、複数工具間の加工面高さの不一致、加工中の工具摩耗、機械の発熱や機械周囲温度の影響による機械や工具、ワーク等の熱変位などが金型の加工精度の誤差要因となる。
これらの誤差要因を撮像式工具測定システムによって抑制できるかどうかを検証するため、テストワークを考案し加工を実施した。加工条件を表1に示すが、6種類の径および形状の異なる工具を異なる回転数で、タイル状に同一高さを狙って加工した。加工中数回工具長測定やワーク基準面高さ測定を入れて、複数工具の工具長の差、工具摩耗、熱変位をキャンセルするようにしているが、ポイントはワーク測定に使用するプローブの長さを都度撮像式工具測定システムにて機上測定していることにある。
工具番号 | 工具種類 | 主軸回転速度(min-1) |
---|---|---|
1 | R3ボールエンドミル | 16,000 |
2 | φ2フラットエンドミル | 20,000 |
3 | R2ボールエンドミル | 26,000 |
4 | φ1フラットエンドミル | 32,000 |
5 | R0.5ボールエンドミル | 40,000 |
6 | φ0.3フラットエンドミル | 40,000 |
表1 テストワーク加工条件
従来ワーク測定および工具測定においては、プローブ長や工具長測定装置の高さ、機械原点の主軸とテーブル間の距離などは固定値として扱い、その数値を用いてワーク高さや工具長を算出している。しかしながら機械の発熱や機械周囲温度の影響によって当然これらの寸法も熱変位するので、測定誤差が生じてしまう。そこで前述のようにプローブ長を工具測定装置にて測定することによってそれらの誤差を相対的にキャンセルさせるのである。
実際にワーク加工した時のプローブ長、ワーク座標値、工具長および機械周囲温度の測定値を図2に示す。ワーク加工には合計4日間かかっているが、連続で加工したのではなく、1日約8~10時間加工後機械の電源を落とし、翌日機械の電源を入れて加工の続きを再開している。機械周囲温度の変化が最大5℃もあったこともあり、プローブ長測定値は最大21μmの変化があるが(前述したようにプローブ自身の熱変位のみならず機械や工具測定装置の熱変位も含まれている)、これを固定値としていた従来の方法では、この数値分の誤差が発生していたことになる。
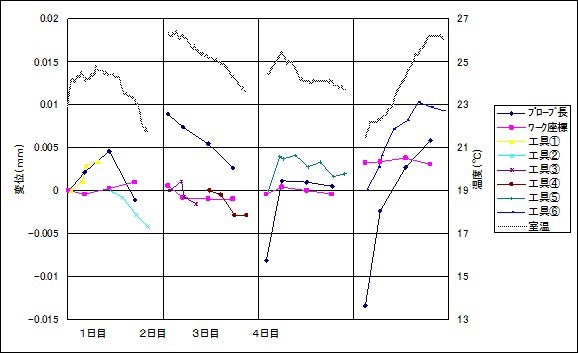
加工後のワークの上面の段差を測定した結果を図3に示す。6種類全ての工具の加工面のあるラインにおいて、段差は±2μm以内に全て収まっており、撮像式工具測定システムによる誤差抑制の効果を確認することができた。
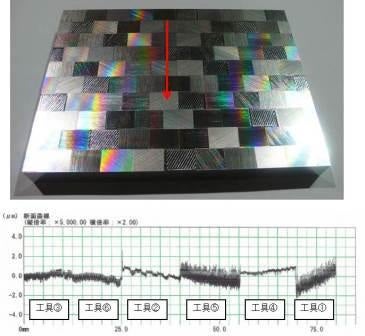
まとめ
小型精密加工機μV1による「撮像式工具測定システム」を用いた高精度の加工事例を紹介した。従来、加工途中で機械の電源を落とし、日をまたいでしまったら精度を再現することは不可能であると考えられていたが、その通念を変えることができた。これを用いれば、一度加工した後の修正加工、追込み加工も高精度で実現できると考えられる。今後も市場のニーズに応えるべく、更なる機械や機上測定などのアプリケーションの高度化を追求し、製造業の発展に少しでも貢献できるよう努める所存である。
※「型技術2011年2月号」掲載論文