NIDECの技術力
半導体ウエハー搬送ロボット
革新的な3Linkアームで省スペース化に貢献
スマートフォンやパソコン、自動車など身近な機器から、通信ネットワークなどの社会インフラまで。半導体は産業を支える基盤といっても過言ではありません。その製造工程は多く、極めて高いクリーン度が求められます。NIDECグループでは、半導体の製造現場向けに、基板(ウエハー)を搬送するロボットを製造しています。
前工程から丸形のウエハーを受け取り、次の工程へと運ぶロボット。近年、クリーンに保つ空間を狭く抑えることや、限られたスペースにより多くの半導体製造装置を設置するため、コンパクト化の需要が高まっています。
NIDECグループが開発した半導体ウエハー搬送用のウルトラクリーンロボット「SR8241」シリーズは、独自の3Link構造による3アームを実現。他社は2つのリンクを用いた2アーム方式であるのに対して、3アームであれば、それぞれのアームを短く抑えられるため、可動範囲を72mm短くすることに成功しています。10mm単位でコンパクト化が求められる半導体製造装置の世界に、非常に大きなインパクトを与えています。
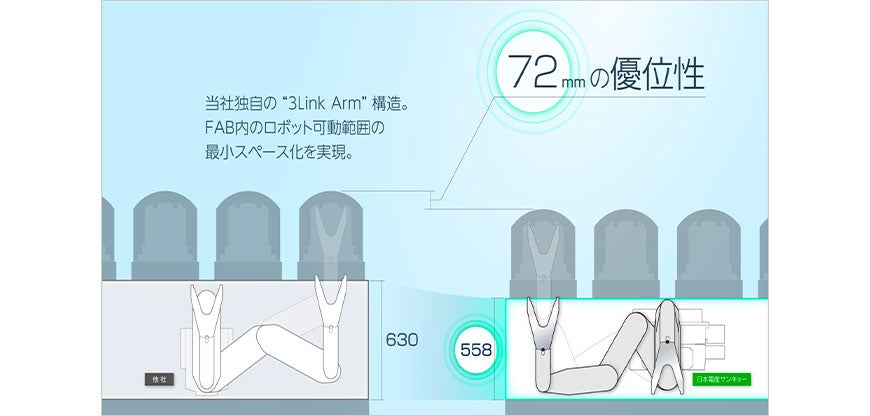
搬送用ロボットは前後に4つずつ並んだカセットの間を行き来するように動きますが、可動範囲を狭くすることで半導体製造装置そのもののサイズをコンパクトに抑えられます。また、アームの全体長はむしろ長くなっているため、将来的に並ぶカセット数が増えても、3アームであれば対応がしやすいというメリットもあります。
可動するリンク部分はモータによって制御されます。「SR8241」では制御するリンクの数が増えていますが、使用するモータの数は2アームタイプから増えていません。そのため、コストアップは最小限に抑えられます。
3Link構造を支えるクリーン技術
半導体製造の現場では0.1ミクロンレベルの微細な粒子(パーティクル)が大敵となります。そのため、クリーンルームで製造されますが、製造装置そのものもパーティクルの発生源。特に金属やゴムが擦れ合うベアリングやオイルシールのあるロボットの可動部は大きな発生源です。
その発生源であるアームのリンクを増やすことができたのは、クリーンな大気中にパーティクルを放出しない技術があったためです。関節部には独自のシール構造が採用されており、パーティクルの放出を防ぎます。
ロボットの底部には排気ファンを装備。ロボット内部にダウンフローの気流を発生させ、パーティクルを床下に排出します。また、ウエハーガイドの可動部でもパーティクルが発生しますが、ロボット内部に真空を作り出すことで吸引する機構を採用し、空間をクリーンに保ちます。こうした技術により、「SR8241」はISO規格のクリーンルームのクラス分けで、最も清浄度の高いクラス1を取得しています。
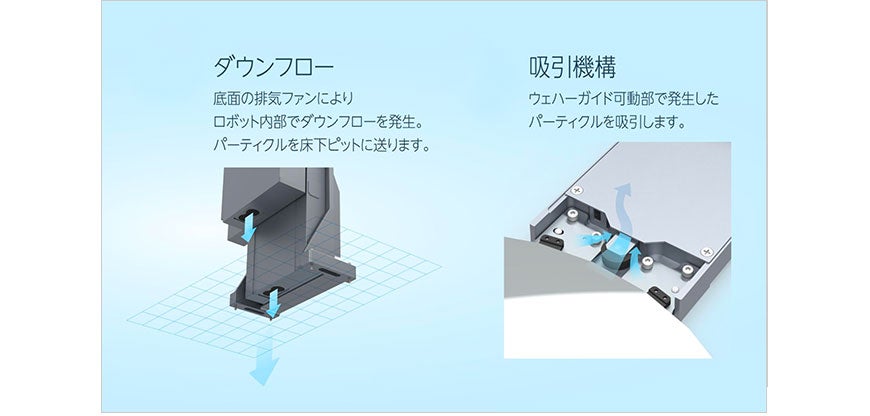
こうしたクリーン技術により、可動部からパーティクルを放出しない構造を実現したことで、可動部を増やす3Link構造を採用することができました。
シンプルな動作で高い耐久性を確保
リンクの数は3つに増えていますが、アームの動きはシンプルにできるため、リンクごとの動作量は抑えられています。そのため可動部にかかる負荷を抑えることが可能となり、高い耐久性も確保。ロボットには5年ごとのオーバーホールを推奨していますが、「SR8241」では機器の信頼性を表すMTBFで5年以上を実証しています。
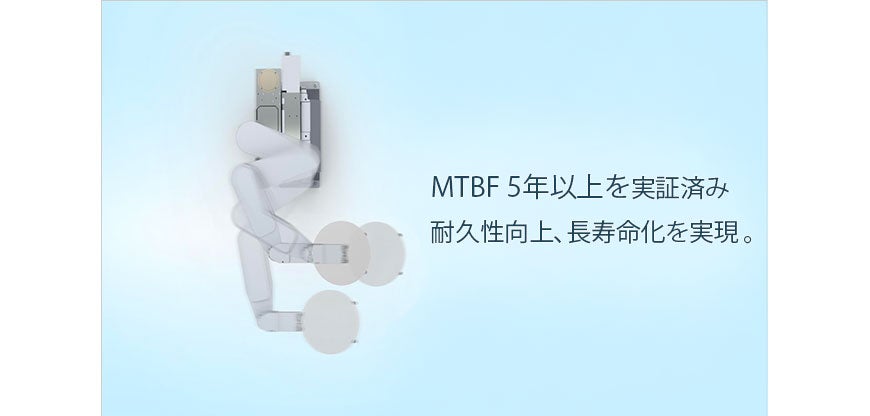
グループ企業が連携することで、キーパーツであるモータをスピーディに調達できるだけで全体のバランスに優れた設計が可能となりました。高い信頼性は、NIDECグループのチーム力に裏付けられているといえます。