Quest For Motors' Hidden Abilities and New Potentials
Lecture 5: Ultrasonic Motors—Mimicking the Movements of Human Hands
Numerous types of motors exist, and motors of different sizes and characteristics are produced based on their applications. Almost all motors use current and magnetic forces, and they are collectively called “electromagnetic motors.” There are other types of motors, electrostatic and ultrasound motors. I explained towards the end of my last article that there is an ultrasonic motor, with no gap between its stator and rotor.
This article explains the ultrasonic motor, in comparison with the other two motors, electrostatic and ultrasonic motors.
Table 1 shows a list of comparison of these three types of motors. The table features a permanent magnet brushless motor.There are various type of electrostatic motors, among which is an actually produced motor, developed by Mr. Toshio Sashida.
There are many ways to explain an electromagnetic motor’s force and the principle of its rotation force. This article explains that the electromagnetic line reaching a permanent magnet rotor’s surface is slightly tilted, and that the magnetic line-generated tangential force acts. A tangential force is proportional to the product of the radial componentmultiplied by the tangential component
which is generated by the current flowing through a stator’s winding wire.
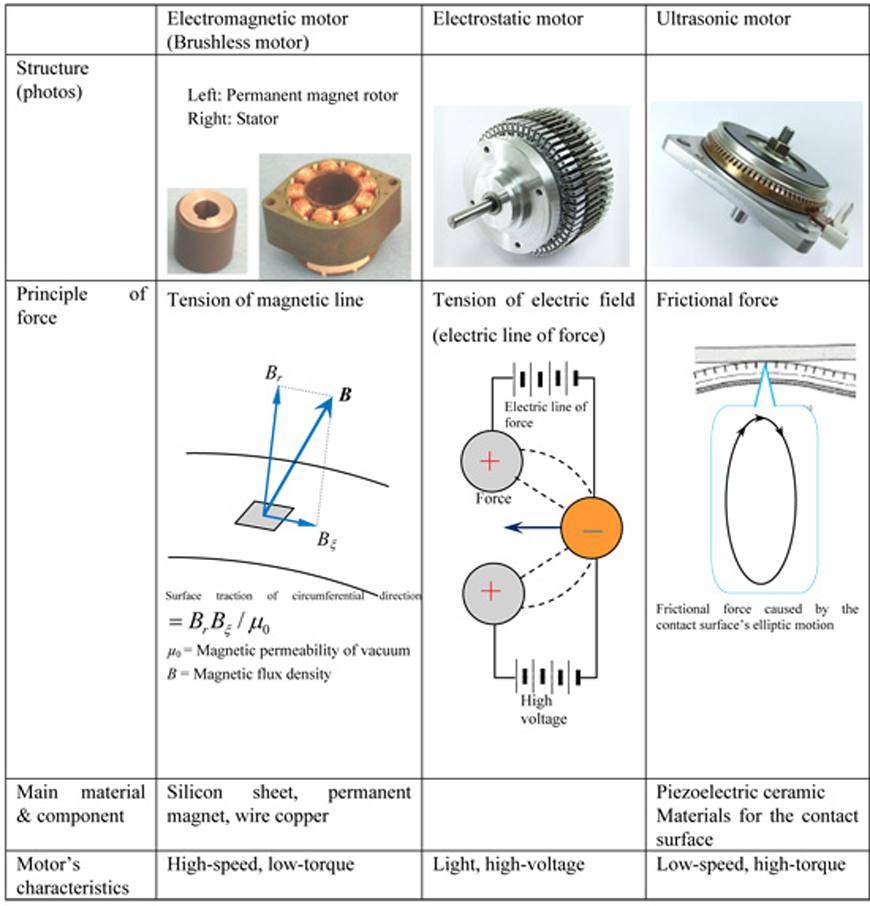
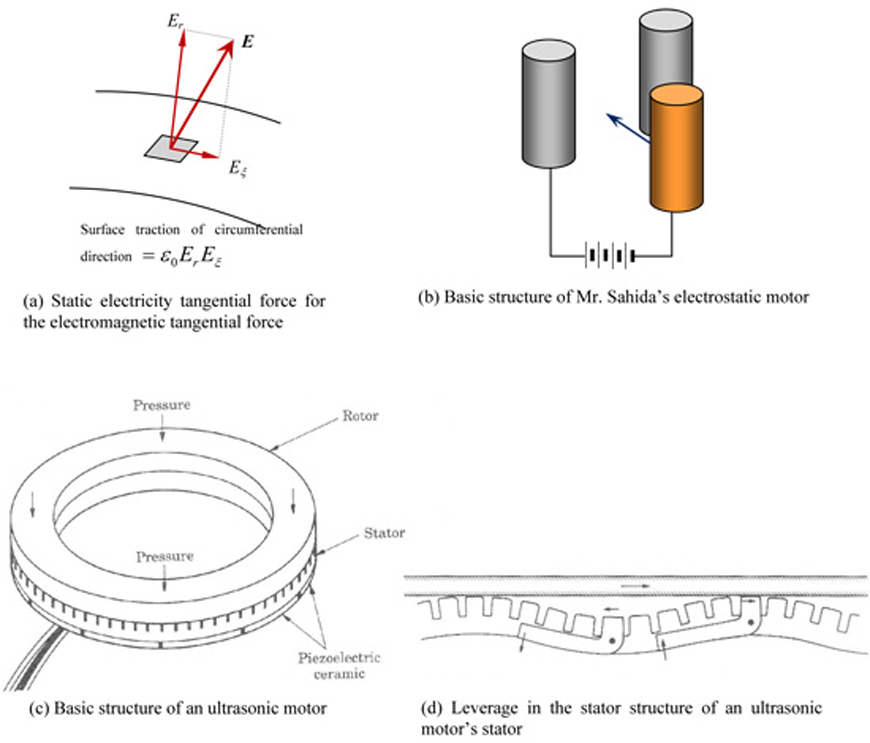
Similarities and differences of these three types of motors
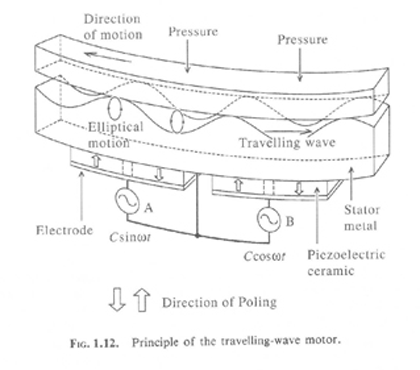
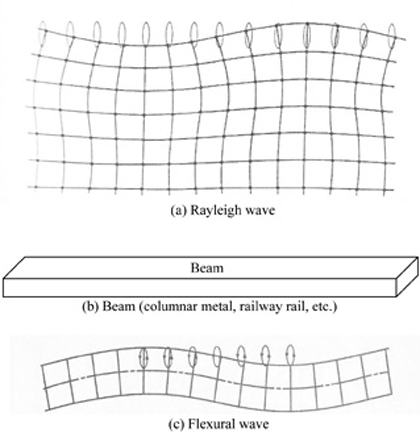
a Rayleigh wave and a beam
One similarity between electromagnetic and electrostatic motors is that torque acts either both in a vacuum and through a void, whereas an ultrasonic motor rotates, as shown in the structural mechanism in the far right of Chart 1, by using the frictional force generated by contacting the surfaces of its rotor and stator.
One similarity between electrostatic and ultrasonic motors is that they do not use a magnetic field.Part of ultrasonic motors’ fundamental nature is similar to that of electrostatic motors in that the former motors use elastic piezoceramics in some electric fields. “Piezoceramic,” a type of ceramics, are extremely hard insulators, and yet they expand and contract, though slightly, when voltage is applied to them. Using this phenomenon enables the generation of an elliptic motion on a metal ring’s surface. Supplemental Figure 1(c) shows thin piezoceramics used in an ultrasonic motor’s basic structure. Mr. Sashida discovered that the displacement of a metal increases when it is resonated with applied voltage used as an ultrasonic range, and that he can create not just simple expansions and contractions but waves. The grooves on the ring-shaped stator metal are, as shown in Supplemental Figure 1(d), to enhance the movements on the contact surface’s elliptic motion (indicated with arrows (← →)).Fig. 2 describes a concept, not a principle mechanism, that when two-phase AC voltages (and
) are applied to two pairs of piezoceramics (A and B) respectively, longitudinal transverse waves that each rotates clock- or anticlockwise on the ring’s surface. This concept illustrates that a Rayleigh wave was considered in Mr. Sashida’s process of invention.A Rayleigh wave, which appears on a land surface or a hard metal’s surface like an earthquake-caused shake, is shown in Fig. 3. Contemporary ultrasonic motors utilize the flexural waves propagated to a thin metal.
MEMS
Small electromagnetic motors are sometimes called “micro motors.” These motors drive a robot’s hand fingers, move a wristwatch’s hands, vibrate a mobile phones, etc. It is difficult, however, to produce such a motor that is 1mm or less in diameter or length, and its efficiency will remain low even if its wires are wound successfully. On the other hand, electrostatic motors, even if made in a small size, can maintain their efficiency high enough. Microscopic electrostatic motors, which are attracting people’s attention as MEMS (Micro Electro Mechanical Systems), are becoming a large industry. The drive voltage of MEMS, made of silicon and produced the way semiconductors are made, does not increase tremendously.
MEMSs, which as electrostatic actuators utilize the voltage generated by the micro nozzle of an ink-jet printer’s head or by pressure-caused displacement, are used not for rotation motion-related applications but for pressure, acceleration and flow rate sensors, HDDs’ heads, optical switches that control a small mirror to switch an optical path, and other products.
Ultrasonic motors’ characteristics
Ultrasonic motors, which use mechanical frictions, have a short durability if operated consecutively. This is why ultrasonic motors are used for non-consecutive operations, and have the following five advantages:
(1)No gear wheels needed. Low-speed and high-torque. High responsiveness
(Electromagnetic motors, on the other hand, are designed to be high-speed, low-torque motors to improve their efficiency, and also to work as low-speed, high-torque motors as necessary by the use of a speed-reduction mechanism).
(2)Quiet
(Ultrasonic motors, without a gear wheel or other speed-reducing mechanism, vibrate quietly in an ultrasonic range).
(3)Suitable for small products. Light, thin, short, and compact
(While electromagnetic motors become less efficient as they become more and more compact, ultrasonic motors can maintain high efficiency even in a small size).
(4)Free from a ferromagnetic field’s effect
(Ultrasonic motors are most suitable as actuators to inject a contrast agent for an MRI (medical equipment)).
(5)Can be made in a hollow construction
(Ultrasonic motors are suitable for a camera’s autofocus function).
Comparison of the three types of motors
In 2010 or so, I visited Mr. Sashida’s company (Shinsei Corporation), and discussed the characteristics of the three types of motors, covering various topics including the F5B brushless motor, the product we developed at Nidec Research and Development Center.
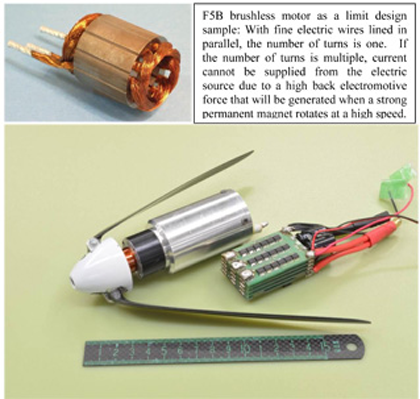
a drive control circuit.
A 300A current is sometimes supplied
with a 24V electric power supply.
“Mid- and large-size motors, including those to generate power, are predominantly electromagnetic. What if one makes a compact, high-output motor?” This question led Mr. Sashida to invent an ultrasonic motor in 1976. Almost 40 years ago, compact electromagnetic motors would only have a small output. Prior to the emergence of contemporary ultrasonic motors, Mr. Sashida invented the cuneate ultrasonic motor (SeeFig. 5), which had a strong output for an ultrasonic motor available back then.
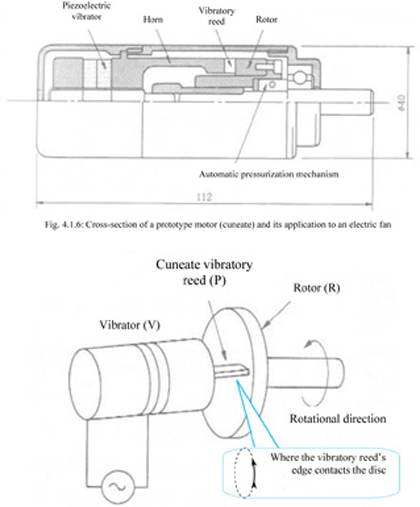
ultrasonic motor, where the edge of
a vibratory reed (wedge) moves elliptically,
and contacts the rotor disc only for the distance
illustrated above.
In a limit-design comparison, an electromagnetic motor’s weight/output performance exceeds that of an ultrasonic one.One of the reasons that Mr.Sashida started to become passionate about electrostatic motors after ultrasonic motors was to create a light-weight motor that can operate consecutively.In an electromagnetic motor, its iron core to allow the magnetic field through and its copper to allow current through make the motor heavy, whereas electrostatic motors, in principle, can be made lighter by using its materials effectively.
Both electromagnetic and ultrasonic motors are difficult to use in a vacuum.Electromagnetic motors do not operate properly unless heat is removed by the motor’s winding wire and iron core. The motors need to be cooled down, which can be done with the wind, but there is no wind in a vacuum. Metals, when contacted with each other in a vacuum, may bind together. Metals and a sliding agent contact one another in an ultrasonic motor, which makes it difficult to choose materials that work properly in a vacuum.
Only few components of an electrostatic motor heat up, which makes the motor efficient.
To summarize all the points above:
(1)There is a wide variety of motors, but they are overwhelmingly electromagnetic (in terms of motors’ characteristics).
(2)There are ultrasonic and electrostatic motors, which are supplementary to electromagnetic motors. Not so many of ultrasonic and electrostatic motors, however, are in practical use.
(3)Ultrasonic motors are suitable for applications where a low-speed, high-torque is required instantly, without using a reducing mechanism (e.g. cameras’ autofocus function).The motors are optimum as actuators necessary in a ferromagnetic field (e.g. an MRI’s contrast agent injection unit (an injector).
(4)Electrostatic motors are suitable for use in a vacuum.
Lastly
Mr. Sashida decided to invent an ultrasonic motor because there was no compact and yet strong motor for actuators for human hands or robots.Though the ultrasonic motor was invented, motors for a robot’s hand fingers have not been invented yet.
To see an actuator for a robot’s hand fingers requires us to wait the emergence of a genius scientist who tries to invent such a product as his lifework. My next article will focus on the development of semiconductor devices that led to the birth of a new motor, followed by actuators for hand fingers.
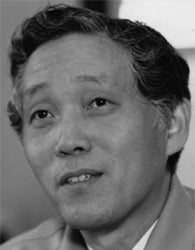
(physicist and inventor)
(circa 1990)
Besides Mr. Shigenobu Nagamori, the founder of Nidec Corporation, the person whom I met in my motor-oriented life and who impressed me with his tremendous tenacity is Mr. Sashida, the inventor of the ultrasonic motor who started business on it. When the two appeared as speakers at a 1983 Motortech Japan Symposium, each of the 300-capacity venues was packed with a passionate audience. The industrial history shows that there were always brilliant inventors and business people in a nation when it was flourishing. Messrs.Nagamori and Sashida are such symbolic figures in Japan’s motor history.
When I visited Mr. Sashida in 1981 at Shinsei Corporation, which was located opposite of Roka Park and along Ring Road No. 8 as the chairperson of this symposium’s planning committee, I felt that “I had met the real physicist.”It was tremendously impressive to see a motor, which Mr. Sashida had named the “wedge-type motor,” swiftly rotating an electric fan’s propeller.On my second visit the following year, Mr. Sashida showed me a new model, called the travelling-wave motor. He had a brilliant mind far superior to that of a scientist to examine longitudinal and transverse Rayleigh waves (which are described in any physics textbook), carefully analyzing a beam’s wave (a material mechanics subject), and develop the concept of using piezoelectric elements to generate a rotating electric field and creating a rotational wave. His image overlapped with that of Michael Faraday, who discovered electromagnetic induction.
Precision machining should be essential to manufacture this motor, but Mr. Sashida’s workshop was on the second floor of an old, wooden building, whose floor would be shaken by large trucks constantly passing by. Mr. Sashida was using a wrapping machine to create a flat surface.According to him, “Tools to make precision products do not necessarily need to be precision.The human history of making precision products proves this statement.”Mr. Sashida was making sure not to make unnecessary expenses while engaging in his motor development.
In 2010, when Mr. Sashida started renovating the main entrance to his company building, he found its columns to be battered.Thinking that a company operating in a building under such a poor state would eventually be unable to fulfill its responsibilities as the world’s only manufacturer of medical ultrasonic motors, Mr. Sashida decided to construct a new company building, with three stories above the ground and one basement floor.