Implemented Solutions
Helium-Filled Hard Disk Drives
Improved Read/Write Precision and Lower Power-Consumption with Helium-Filled HDDs
Although HDD areal density has been increasing in the past as a result of refined magnetic heads and innovative recording methods, the very air inside the HDDs—internal components of hard disk drives are usually exposed to the same air that surrounds the HDD itself—stands in the way of further progress. The air resistance experienced by the disks as the HDD spindle motor rotates at speeds of several thousand or even tens of thousands of revolutions per minute leads to vibration, which in turn negatively affects the read/write precision of the HDD.
In addition to improving read/write precision, reducing the vibration of the disks by decreasing the drag would also allow them to be made thinner, increasing the number of disks that can be fitted inside a single HDD. As an added bonus, the electricity consumed by the spindle motor as it rotates the discs would decrease as well.
Determined to make this happen, Nidec set out to test an entirely new concept: hard disk drives filled with helium instead of air in order to reduce drag.
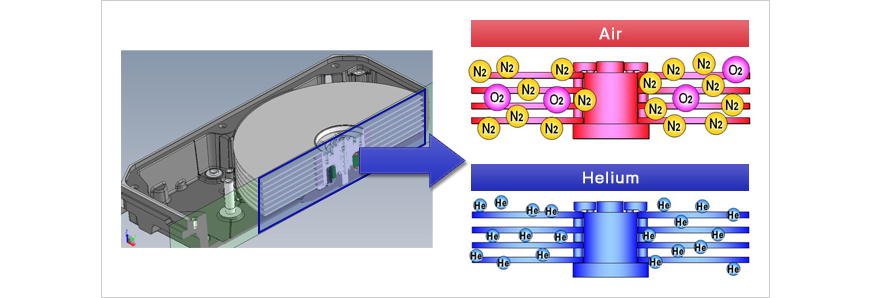
On the one hand, the low density of helium—only 1/7 that of air—results in considerably less drag, but on the other hand a new problem arises as helium atoms—due to their small size—have a tendency to leak through adhesive substances or cavities in the aluminum die casting base plates. Ensuring that the helium stays sealed inside the HDDs for 5 years—the life-span of a hard disk drive—proved to be a particularly difficult challenge.
In order to ensure that the helium does not leak through the 1-2 mm thin base plate, every parameter of the casting process—the shape of each part of the metal molds, temperature control and more—is optimized based on CAE analysis of the flow of molten aluminum during casting. Furthermore, in addition to using vacuum casting, we have developed and adopted a variety of other new technologies as well. As a result, we have succeeded in establishing the technology necessary for mass production of base plates, with very few defects, that can be sealed for 5 years without leaking any helium.
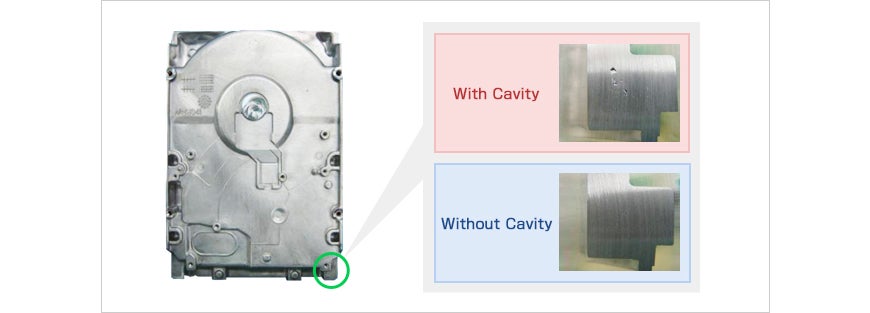
The adhesive used to seal the HDDs is another important factor in preventing helium leakage. After making sure that the adhesive is applied thickly, the individual components are joined together under very high pressure in order to maximize resistance to leakage.
An adhesive with a low outgassing rate was chosen to avoid contamination caused by gases other than helium. Furthermore, the HDD components go through repeated baking procedures—removing gas in advance—during every step of the manufacturing process in order to minimize outgassing from the adhesive and resin etc.
We have also worked together with an oil manufacturer to jointly develop a specialized oil—with a low rate of evaporation and high resistance to external moisture—for the fluid dynamic bearings.
Helium-filled hard disks are a result of numerous small but difficult steps. By making the disks thinner, a single HDD can be equipped with 7 disks, resulting in hard disks capable of storing up to 6 terabytes (as of November 2013) of information making their appearance in the market. At the same time, we have also succeeded in reducing the electricity consumed per unit of data by 50%.
Developer's Comment
High capacity low power-consumption helium-filled HDDs for servers in data centers are selling especially well. HDD manufacturers are pushing the limits with next-generation recording methods, such as heat-assisted recording and multilayer magnetic recording, and HDD capacity is expected to keep increasing in the future as well. At Nidec, we will continue to contribute to the emergence of higher-capacity HDDs by developing new technology, not only for our motors, but for HDD base plates, top covers and their respective materials as well.