Implemented Solutions
Power Steering Motors (1st – 3rd Generations)
Nidec strived for the reduction of cogging torque, which is the largest challenge affecting pure electric power steering systems.
Nidec overcame multiple problems one after another by applying accumulated technologies and creativity to develop solutions.
A pure electric power steering system is considered to have high fuel efficiency because the motor is directly coupled with the steering shaft and the steering is assisted by the motor. However, the cogging torque affects on the steering feeling of the driver and the reduction of cogging torque is a major challenge. When we first entered the field of the EPS (Electric Power Steering) system, we adopted the distributed winding system that winds copper wires of each phase across the three poles. As the motor specifications were limited by the customer's needs, we had to choose the distributed winding. In order to reduce the cogging but obtain enough output at the same time, we had to use the sophisticated stator structure for high-density windings of copper wires. This motor was developed by the total power of only Nidec which had a huge advantage, not only the design but also in mass production departments for actual motor production.
Nidec successfully entered the EPS field, and the EPS demand extended in earnest. However, we had a problem of EPS which is too complex to mass production. So, we adopted the concentrated winding method and developed a motor having the simple winding structure. Together with the concentrated winding method, we used multiple poles of the motor and converted the torque variation to higher frequency to reduce motor cogging. We adopted the divided core method that winds wires onto divided cores and then assembled those cores. We could use all spaces between cores when winding wires onto divided cores. Therefore, we could wind copper wires in a high density fashion and realize high output.
The mass production of concentrated winding type EPS motors was launched, but the corresponding car model spread to compact cars. New needs to further reduce motor cogging and mass production of new motors emerged. To add to the flexibility in the design with this type of the motor, we significantly changed the conventional ring magnet structure into the segment magnet structure. By closing the magnet to the ideal shape, we could expect to reduce the motor cogging. Together with the adoption of segment magnet, we changed the magnet holding structure so that no adhesives were used, and subsequently we were able to improve both product quality and productivity. Furthermore, to increase the robustness of products on the manufacturing line, we reviewed the core structure to ensure it had minimum tolerance when divided cores were assembled.
First generation
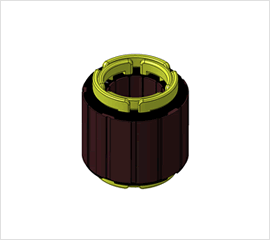
- Distributed winding (with four-pole magnet setting)
- Reduced cogging utilizing divided inner and outer core assembly
Distributed winding type. The distributed winding method was used as the number of poles was limited due to the relationship with the external interface.
Second generation
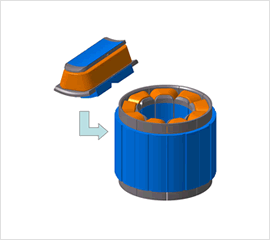
- Concentrated winding
- Divided cores
The wire is wound onto each tooth, and the stator is finally formed.
Concentrated winding and ring magnet type. The simple concentrated winding method was used taking mass production into account.
Third generation
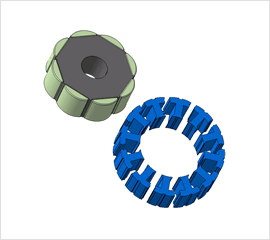
- Concentrated winding
- Divided cores
The wire is wound onto each tooth, and the stator is finally formed.
Concentrated winding and segment magnet type. A segment method that has a flexible magnet shape was used. Devised to eliminate assembly errors.
Comments from developers
As a result, the fuel-saving effect is higher than that of the conventional hydraulic power steering system, and since electric vehicles (EVs) are becoming increasingly popular, it is not an exaggeration to say that EPS is one of the most important business fields in the automobile industry. In these critical fields, Nidec is developing and manufacturing high-performance EPS motors by utilizing our motor design, control and mass production technologies that we have developed over the years. As the leading company in this field, Nidec is making significant contributions to automobile fuel efficiency.